Guided Wave Radar Level Meter
The high-frequency microwave pulse sent by the guided wave radar propagates along the detection assembly (steel wire or steel rod), and meets the medium to be tested, which is reflected due to a sudden change in thedielectric constant, and part of the pulse energy is reflected. The time interval between the emitted and reflected impulses is positively proportional to the distance of the medium to be tested.
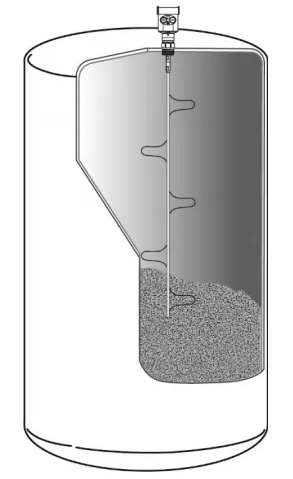
Characteristics:
Thanks to the advanced microprocessor and the unique Echo Discovery - echo processing technology, the guided wave radar level meter can be applied to various complex operating conditions.
A variety of process connections and types of detection components enable the 70X series guided wave radar level meters to be suitable for various complex operating conditions and applications. Such as high temperature, high voltage and small dielectric constant dielectrics.
It adopts pulse operation, and the guided wave radar level meter has extremely low transmission power, can be installed in various metal and non-metal containers, and is harm-free to human and environment.
Description:
The guided wave radar is a measurement instrument based on the principle of time trip. The radar wave operates at the speed of light, and the operation time can be transformed into a level signal through electronic components. The probes emit high-frequency impulses and travel along the cable-type or pole-type probes, which are reflected back and received by the receiver in the instrument when the impulses meet the surface of the material, and transform the distance signal into a level signal.
The reflected impulse signal is transmitted to the instrument electronic line part along the cable-type or pole-type probe, which is processed by the microprocessor to identify the echo generated by the microwave pulse on the surface of the material. Proper echo signal identification is done by the impulse software, with a distance D from the surface of the material and a time travel T of the impulse being positively regular:
D=C×T/2
where C is the speed of light
The distance E of the empty can is known so the level L is L=E-D
Set by entering empty can height E (= zero point), full can height F (= full scale) and some application parameters, the application parameters will automatically adapt the instrument to the measurement environment, corresponding to the output of 4-20 mA.
Measurement scope:
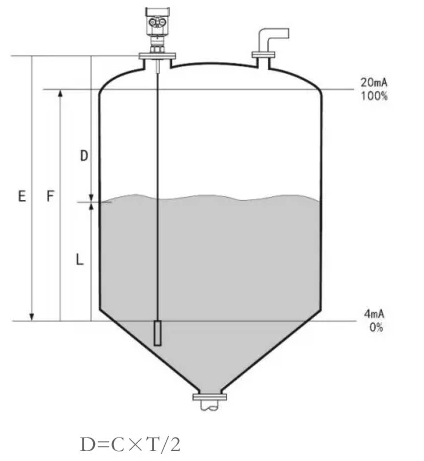
The top blind zone refers to the minimum distance between the highest material surface of the material and the measured reference point.
The blind zone at the bottom refers to a distance that cannot be accurately measured near the bottom of the cable.
The distance is effectively measured between the top and bottom blind zones.
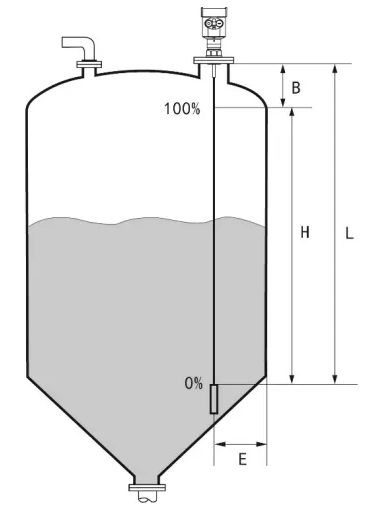
Note:
Reliable measurement of the position in the can only be ensured when the material is between the top blind zone and the bottom blind zone.
Installation guidelines
Be sure that the cable or pole should not come into contact with internal obstacles throughout the range, so avoid the facilities in the can as much as possible during installation, such as ladders, limit switches, heating equipment, bracket and so on. In addition, it should be noted that the cable or pole shall not intersect with the flow of added materials.
Notes for installation:
Avoid the highest material level entering the blind zone of the measurement; the instrument must be kept at a certain distance from the can wall; the instrumentation shall be installed so that the direction of the cable or pole is vertical to the surface of the medium to be tested as much as possible. The instrumentation installed in the explosion-proof area must comply with the national installation regulations for the explosion-proof hazardous area. The shell of Exia is made of aluminum. Exia instruments can be installed in places where explosion prevention is required, and the instruments must be connected to the ground.
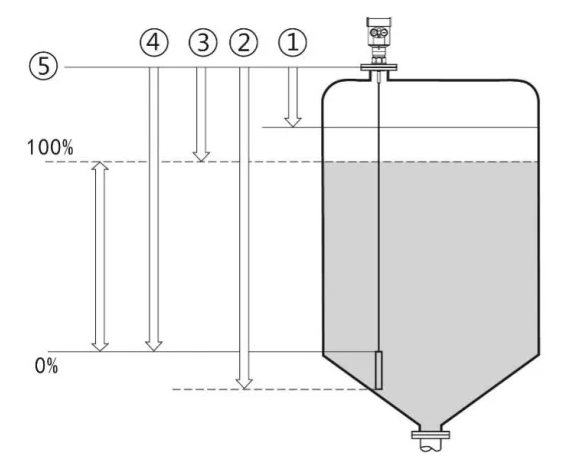
Installation location:
Ø Keep it as far as possible from the outlet and inlet.
Ø Avoid contacting with the wall and bottom of the metal can within the entire range.
Ø It is recommended to be installed at 1/4 or 1/6 of the diameter of the bin, and the minimum distance from the can wall is 1/10 of the measured range.
Ø The minimum distance between the cable or pole probe and the can wall is ≥ 300 mm,
Ø The bottom of the probe is ≥ 30 mm from the bottom of the can.
Ø The minimum distance between the probe and the obstacle in the can is ≥ 200 mm,
Ø The center of the top of the can be installed if the bottom of the container is conical.
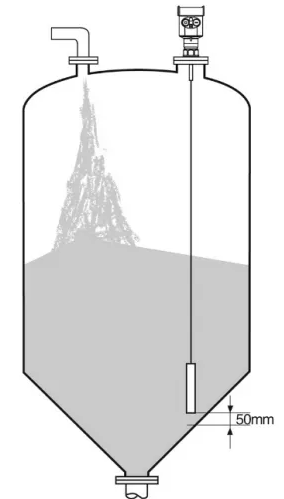
Characteristics of pole radar level measurement:
Ø Any medium with a dielectric constant of ≥ 1.8 can be measured.
Ø It is generally used for media with a viscosity of ≤ 500 CST and is not prone to adhesion.
Ø The maximum range of the pole radar can reach 6 meters, which is mainly used for the measurement of liquid level.
Ø It has a strong penetration capability on steam and foam and is not influenced in the measurement.
Ø For liquid measurement environments with large foams, a single bar guided wave radar level meter should be selected for measurement.
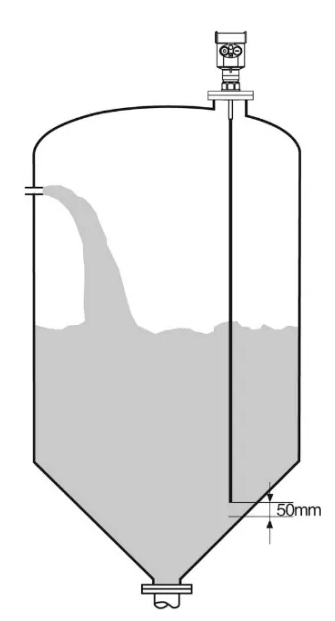
Characteristics of Dual-Cable Radar Level Meter:
Ø For liquids and light solid powders with small dielectric constants, a dual-wire guided wave radar level meter can be used to ensure accurate measurement.
Ø Any medium with a dielectric constant of ≥ 1.6 can be measured.
Ø It is generally used for media with a viscosity of ≤ 500 CST and is not prone to adhesion.
Ø The maximum range of the dual-cable radar level meter can reach 30 meters.
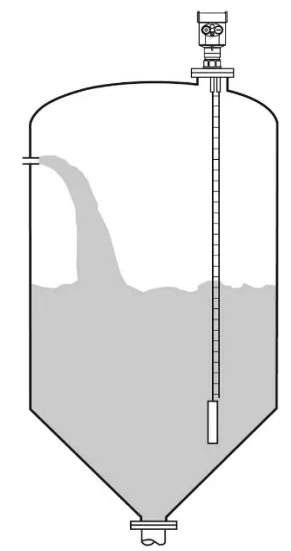
Installation method
Reasonable installation ensures long-term reliable and accurate measurement of the instrument:
The guided wave radar level meter is connected by thread and flange and can be installed on the short pipe. The smaller the diameter of the installed junction pipe, the shorter its length is, the more stable the measurement will be. The height of the installation short pipe should be ≤ 200 mm when the diameter of the installation short pipe is from 2″ to 6″. If the short pipe is installed with a long one, it is best to shorten the short pipe or lengthen the shielding section of the sensor.
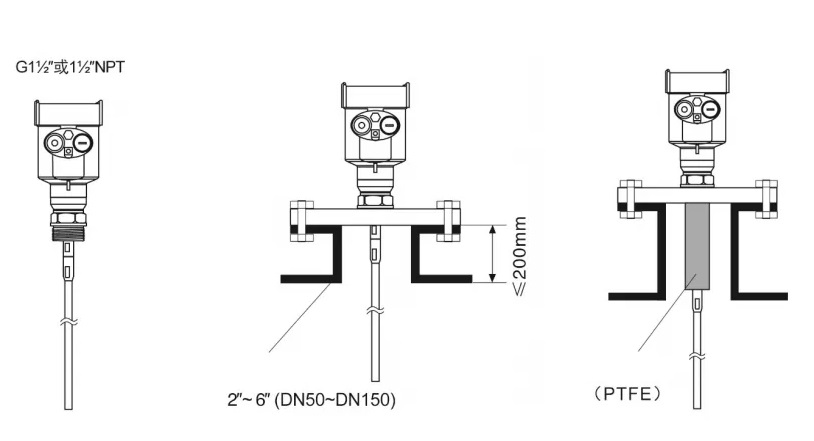
Installation in short pipe of DN200 or DN250:
An echo will be generated on the inner wall of the short tube when the guided wave radar is required to be installed in the short tube with a diameter of more than 200 mm, which will cause measurement errors in the case of low dielectric constant. Therefore, for a short pipe with a diameter of 200 mm or 250 mm, a special flange with a "horn Antenna interface" is required.
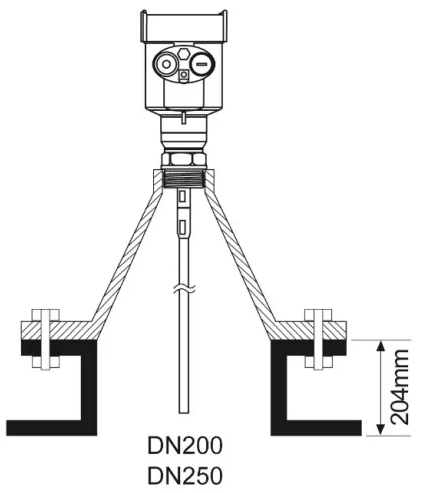
Installation on a plastic can:
Whether it is in the form of a cable or pole, the process connection surface is generally metal if the guided wave radar is to work properly. When the wave guide radar is installed on the plastic can, the instrument needs to be equipped with a metal flange when the top of the can is also made of plastic or other non-conductive materials, and a metal plate if the threaded connection is used.
Installation instructions
² The length of the pole-type probe can be up to 6 meters, and for reservoirs with a measurement distance of more than 6 meters, a cable-type probe can be selected.
² A waveguide can be installed for measurement in case the can is filled with obstacles or is too close to the probe sensor.
Draw force on the rope
During feeding and discharging, the medium exerts a pulling force on the rope probe, the size of which depends on the following factors:
A. Length of the rope B. Densities of the materials C. Diameter of the storage bin D. Diameter of the rope
Optimization of interference
² Interference echo suppression: Programming and debugging software can realize the suppression of interference echoes, thus achieving ideal measurement.
² For media with a viscosity of not more than 500 cst (only applicable to liquids), a by-pass or waveguide can be used to avoid interferences.
Ø Installation of low dielectric constant liquids
For media with a dielectric constant greater than 1.3, a viscosity ≤ 500 cst and less adherence, a waveguide can be installed for measurement, which can achieve the following effects:
² Excellent reliability and accuracy
² It can be used in any medium with a dielectric constant of ≥ 1.3, and the measurement is independent of the conductivity of the medium
² Obstacles in the can and the size of the short tube will not affect the measurement
Corrosive medium measurement
If measuring corrosive media, it is possible to use pole-type or cable-type probe sleeves PTFE and PFA sleeves for measurement
Instructions and precautions in installation:
Ø For the guided wave radar with over long cable in use on site, it is necessary to cut off the spare part of the cable to ensure proper measurement and not knot or wrap or attach the cable to other objects.
Ø When cutting off the cable, it is necessary to cut off the power supply of the instrument, remove the cable, remove the screw on the weight, and intercept from the bottom of the cable. After the cutting is finished, the weight should be reinstalled. After the installation, turn on the power supply and reset the parameters.
Ø For the cable guide wave radar with casing, it is forbidden to intercept itself when the Cable is too long and needs to return to the original factory for intercepting.
Ø For instruments installed in the waveguide, the insulation bracket is required to fix the radar probe to ensure that the radar probe (rod/cable) is concentric with the waveguide, otherwise the measurement will be influenced by the generation of shock or false echoes.